Quality conscience project managers and engineers understand that when looking for a solutions provider, quality certifications are vitally important. Top of mind certifications, like ISO-9001, ensure reliable manufacturing, processing, and testing of end products before they’re packaged up and shipped out the door. In the embedded systems and electronics world, there is another quality certification called IPC-A-610 which is an international source for end product acceptance criteria for high reliability electronic components. This certification allows quality conscience decision makers to rest easy with their choice of embedded systems supplier knowing that all IPC-A-610 certified technicians and production employees are trained not only to spot and correct any physical defects, but also how to handle the end product to maximize life and dependability in the field. Home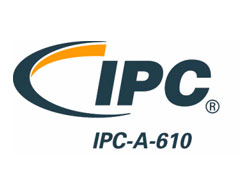
IPC-A-610 holds manufacturing technicians to a higher standard for testing and inspection. These trained Certified IPC Specialists (CIS) possess the knowledge to identify defects which could cause latent or immediate malfunction. Examples of such defects include:
A missed cold solder joint (pictured) could cause a latent power failure in the field due to the solder bond cracking.
- Cracked components, which pass initial inspection, break under the forces experienced in the shipping and receiving process.
- Loose solder balls that when dislodged, can cause a short between traces on the PCB board and result in damaging sensitive components and board failure.
All CIS are trained to carefully detect all of these issues, among others, to ensure the embedded system performs reliably in the field. On top of spotting and correcting any physical defects, they are also trained to be careful when handling the boards to maximize the life of the board in the field. This is important, since a small percentage of a boards life is diminished every time a soldering iron or non-ESD protected person touches it. CIS understand that even oils and salts from their fingers can contaminate the board, causing latent issues.
There are three classification standards for the accept/reject criteriadefined by IPC: Class 1 being general electronic products where the only requirement is to function, Class 2 being dedicated service electronic products where continued performance and extended life is required as well as uninterrupted service is not critical but desired, and Class 3 being high performance/harsh environment electronic products where continued high performance or performance-on-demand is critical to the working end product and must not fail, such as a life support machine at a hospital. All CIS are trained for all three of these classifications for the utmost quality assurance.
Highly reliable embedded system deployments start with choosing a partner who not only carries certifications for manufacturing, process, and designing through ISO-9001, but also employs highly trained, IPC-A-610 certified technicians and production personnel to ensure proper handling and repair throughout the entire process.
Here at Technologic Systems, we pride ourselves in our product quality, ensuring our customers get the highest quality end product. Our entire production team is not only IPC-A-610 certified, they are passionate about quality, keeping up to speed on new quality standards to ensure top level performance and life out of our products. We take extensive care in making sure that the product is carefully handled and meets the highest acceptance criteria so that our customers will be getting what they deserve.
“IPC training has given me greater knowledge and understanding of what can cause a latent problem on boards in the near or distant future. Before going to training I would say that you could consider me to be meticulous with the quality of the product I am working with. But I didn’t realize that even something as small as the oils on my hands can cause latent problems for the board. I also learned that there is a long-term cost to making repairs so that on components with metalization loss it’s actually better not to repair it if the loss is still within the acceptable range.” — Camron Vogelzang, Repair Technician Home